XPAR Vision has led the development of hot end sensors for improved glass container glass forming for 20 years. After four years of co-operation with swabbing robot supplier Novaxion from France, XPAR Vision has launched its own BlankRobot equipment.
As its name suggests, the BlankRobot is designed not only for swabbing but for other applications as well. For swabbing, by applying a special lubricant together with a highly precise application, the frequency is reduced to once every three hours, leaving enough time for the robot to perform other functions. As will be indicated within this article, reducing the swabbing frequency from once every 10-20 minutes to once every three hours will open up many opportunities for the glass container industry.
Forming process stability
With years of experience in developing and actively assisting customers to apply such hot end sensors as the InfraRed Dual camera system (IR-D), automated Gobweight Control (IGC) and GobAssist and Blank side Temperature Control systems (BTC), XPAR Vision provides an accurate and real-time insight to the glass container forming process and its daily disturbances like variations in cullet quality, homogeneity of glass, viscosity, ambient temperature, deterioration of materials, swabbing etc. These disturbances negatively affect glass forming process stability and ultimately cause defects and glass distribution variations in the bottles produced.
Reducing disturbances to the forming process to a minimum and consequently dealing with disturbances when occurring is the main recipe for a stable forming process and a crucial pre-condition for efficiency improvement, weight reduction and/or speed increases.
Swabbing: Remedy or enemy?
For many decades, the swabbing of blank moulds, neck rings, blow moulds, baffles, deflectors etc. has been adopted as a standard operating procedure in all glass container factories. The biggest and most dominant disturbance at the blank side is the swabbing of blanks and neck rings. For each production run, a scheduled swab frequency is needed to keep the sections running. A carbon layer on the inside of the blank profile keeps the friction between glass and blank low and prevents the hot glass sticking to the blank moulds. At the same time, it optimises the contact between glass and blank surface in order to optimise the heat transfer to ensure proper forming of the parison.
Because of the high frequency of swabbing required, the number of different people involved (multiple groups/shifts) and the brush method used, it is one of the most discussed standard operating procedures in the glass container industry. It is obvious that it is very difficult to get everybody aligned to perform the swab in an identical way. At the same time, health and safety is at stake and an ever-growing concern.
IR-D measurements show the actual impact of the way each operator swabs the blanks. Even the swab interval (frequency by SOP) is precisely shown. In other words, with the IR-D swab performance can be followed at any time.
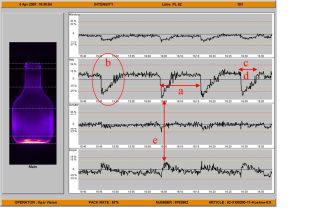
Figure 1 provides an example that shows the (a) frequency, (b) impact, (c) how long it takes before the process stabilised again, (d) how many bottles are affected or should be rejected and (e) the effect for glass distribution in the bottle.
The impact of swabbing to the quality of glass container is strongly correlated. From the example given, it is obvious that swabbing is destabilising the forming process to a great extent, e.g. that the so-called swabbing impact easily lasts for five minutes or more. With a swabbing interval of 15 minutes, this means that the forming process is destabilised 33% of the time due to swabbing. Therefore, it should be concluded that swabbing is more an enemy than a remedy.
Swabbing robot
Swabbing robots have been available to the glass container industry for more than five years. In contrast to manual swabbing, with robot swabbing at least the variation due to different operators executing the swabbing task is eliminated. The advantages are obvious:
- Better product quality due to consistent and uniform lubricant application
- Savings on swabbing oil.
- Less time spent on swabbing; operators can focus more on other tasks.
- Improved working conditions, with better air quality and increased work safety.
Despite these obvious advantages, the swabbing robots currently available are basically not more than an automated form of manual swabbing. The swabbing frequency itself has not been touched. Still every 5-20 minutes, forming process stability is disturbed. In addition, due to the fact that the robot needs to pass all sections every 5-20 minutes, accessibility to the IS machine without disturbing the swabbing process is extremely limited.
A true revolution
The disadvantages of currently available swabbing robots, together with the known potential of a patented lubricant, were reason for XPAR Vision to develop its own BlankRobot (figure 2). One of its functions, developed in exclusive co-operation with Lubriglass of Germany, is blank mould swabbing and neck ring swabbing. A special and patented lubricant is precisely applied in extremely small amounts, leading to a swabbing frequency of once every three hours, with almost no swabbing impact.
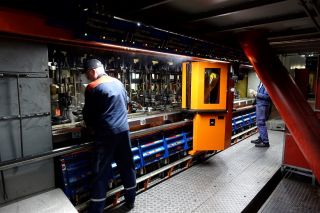
In comparison with traditional swabbing robots, the BlankRobot hardly uses any lubrication (from 100% manually to 25% by swabbing robot to approximately 2% by BlankRobot). Consequently, there is barely any pollution and thus the working environment is much healthier and safer.
Furthermore, because of the extremely low swabbing frequency and low impact by applying very small quantities of lubricant, there is minimal disturbance to the glass forming process. As a result, other hot end sensors will see other process disturbances like changing glass conditioning, mould wear and ambient temperature much more easily and more accurately. This improvement/dedication of measurements will lead to effective feedback loops and logically has huge positive impact on the effectiveness of forming process automation. And of course, there will be a positive impact on the lifetime of (mould) material, as well as the operator time made available for other tasks. The BlankRobot also has time to perform other tasks between swabbing, including baffle and deflector swabbing, automatic alignment of delivery and in-section diagnoses.
Next steps
As with any innovative technology, the current installations at launching customers provide the initial proof of concept, which means that the BlankRobot concept is more than an idea. Market introduction is planned for early 2019. If you are interested about this revolutionary steps forward towards fully integrated forming process control contact XPAR Vision (see details below). Also if you are interested in the ongoing developments of Hot End sensor technologies, keep following our website and subscribe to the newsletter. Or send an email for personal response: contact@xparvision.com.
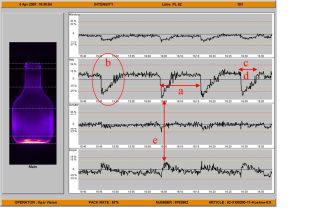