The IGC – Infrared Gob weight Control system – is an add-on to XPAR Vision’s IR-D infrared camera system that assists container glass and tableware manufacturers to increase their glass forming process capabilities by controlling the weight of all cut gobs automatically.
This innovative solution is suitable for all forming processes (Blow & Blow, Press & Blow and NNPB) and for round and non-round ware in each glass colour.
operating principle
At the Hot End XPAR Vision’s IR-D system detects the intensity of infrared radiation emitted by each single hot glass product. The IGC system relates this measurement to the weight of the corresponding gob. Any deviations in gob weight are automatically compensated by the IGC in adjusting the position of the tube and/or the needles.
The IGC ensures a constant weight of each individual gob, thus eliminating an important source of process variation.
The simple and intuitive user interface notifies the operator automatically to weigh the product when needed, in order to reconfirm the weight to intensity correlation.
A special Start-up mode allows for a quick and accurate Job Change execution.
The IGC enables access for any user in the company’s network to review the status of the forming process and the quality of the glass products.
open data interface
XPAR Vision enables open data connections to standard and proprietary Production Information Systems to present and correlate real time hot end information with other production data from furnace, feeder, Cold End inspection and laboratory systems.
Uniquely XPAR Vision teams with major IS-machine manufacturers to provide closed loop interfaces with OEM Feeder systems for automatic weight control of the individual gobs.
capabilities
- Accurate gob weight control (+/- 0.25% weight variation)
- Automatic adjustment of tube height (closed loop)
- Automatic adjustment of needle/plunger position (closed loop)
- Special Start-up Mode for faster Job Change
- Single and tandem IS machine support
- Multi gob support
- Multi weight support
- Multi product support
- Applicable for all glass colours
- Round and non-round ware
- Blow-Blow process support
- Press-Blow process support
- Wide Mouth Press & Blow process support
- NNPB process support
Need more information?
Get in touch with Paul Schreuders (CEO)
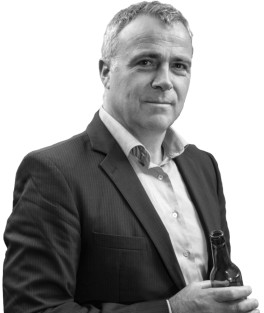
Downloads
Latest shared news and knowledge articles
Glasstec 2024
Want to know what we have to offer? Fill in your name and email and you will be redirected to the right page.
Digital resorting: held ware dramatically reduced!
In every container glass factory held ware and resorting is a pain in the butt, and even getting worse. With XPAR Vision’s Long Term Image Storage this held ware and resorting will be dramatically reduced. Held ware In case of any suspicion for bad quality ...
Multi-view monitoring for automatic gob weight control
Specialising in and leading innovations of advanced sensor and robot technology, XPAR Vision’s products and services help to improve the forming process performance and quality control for the global container glass and tableware industries. Paul Schreuders explains how the company’s latest sensor enhances its portfolio of solutions and offers ...