The IR-D – Infrared Dual camera system – assists container glass and tableware manufacturers to improve their glass forming process capabilities. This results in better product quality and increased efficiency.
The innovative solution is suitable for all forming processes (Blow & Blow, Press & Blow and NNPB) and for round and non-round ware in each glass colour.
operating principle
Immediately after the forming of the glass product the IR-D detects the intensity of infrared radiation emitted by the hot containers. The measured intensity is translated into essential information about the status of the glass forming process and makes accurate defect inspection possible, already in the Hot End.
The IR-D rejects glass products with critical defects before these enter into the annealing lehr. The real-time process information is related to each cavity which helps the operator to take the right remedial actions.
The IR-D enables access for any user in the company’s network to review the status of the forming process and the quality of the glass products.
open data interface
XPAR Vision enables open data connections to standard and proprietary Production Information Systems to present and correlate real time hot end information with other production data from furnace, feeder, Cold End inspection and laboratory systems.
Uniquely XPAR Vision teams with major IS-machine manufacturers to provide closed loop interfaces with IS-timing systems for automatic Ware Spacing and Glass Distribution control.
capabilities
Accurate inspection of critical defects
- Thin bottom
- Bird swing
- Inclusions
- Shape
- Verticality
- Fins
- Wedged bottom
- Choked necks
- Thin neck
- Thin spots (sidewall)
- Hot spots
- Stuck ware
- Fallen ware
- Diameter
- Ovality
- Container position on belt
Real time cavity related information about the forming process
- Glass quality
- Gob condition
- Gob loading
- Mould condition
- IS timing setup
- Cooling
- Section performance
- Swabbing disturbance
- Job Change
- Ware spacing
- Ware positioning
Special functions:
- Critical defect detection to activate special actions
- Operator Assistance by root cause indication
- All image storage for full traceability (short and long term)
- ‘Real-inspect’- sample images for verification of optimized setup and customer audits.
Customer opinion
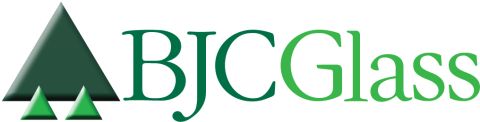
BJCGlass
Thai Glass Industries (TGI), container glass manufacturing subsidiary of Berli Jucker in Thailand, and XPAR Vision from the Netherlands, join forces in a strategic partnership, providing leading Hot End sensor technology to the global container glass industry. The partnership is the crown on the co-operation, …
Read entire storyNeed more information?
Get in touch with Paul Schreuders (CEO)
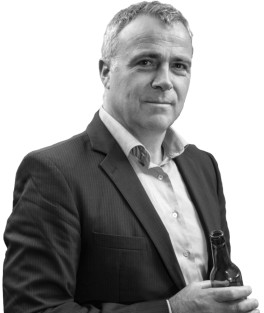
Downloads
Latest shared news and knowledge articles
Digital resorting: held ware dramatically reduced!
In every container glass factory held ware and resorting is a pain in the butt, and even getting worse. With XPAR Vision’s Long Term Image Storage this held ware and resorting will be dramatically reduced. Held ware In case of any suspicion for bad quality ...
Multi-view monitoring for automatic gob weight control
Specialising in and leading innovations of advanced sensor and robot technology, XPAR Vision’s products and services help to improve the forming process performance and quality control for the global container glass and tableware industries. Paul Schreuders explains how the company’s latest sensor enhances its portfolio of solutions and offers ...
European Union, SNN and EZK SUPPORT XPAR Vision DEVELOPMENT
Thanks to the support of the European Union, SNN and the Ministry of Economic Affairs and Climate Policy (EZK) through a EFRO grant, XPAR Vision is able to develop and valorise 2 prototype sensors for glass composition and lateral glass distribution, including integration into a ...