The innovative InfraRed (IR) camera technology for inspection and process monitoring is proving to become a standard for each production line for the production of glass containers. Moreover, combined with closed loop direct interaction with major IS-timing systems, the IR-technology is ready to meet Industry 4.0 standards.
New market entry
In 2018 XPAR Vision also introduced this technology to tableware production. In cooperation with one of the major players in the tableware industry, the IR-D system has been optimized for press-blow tableware production lines for the production of drinking glasses.
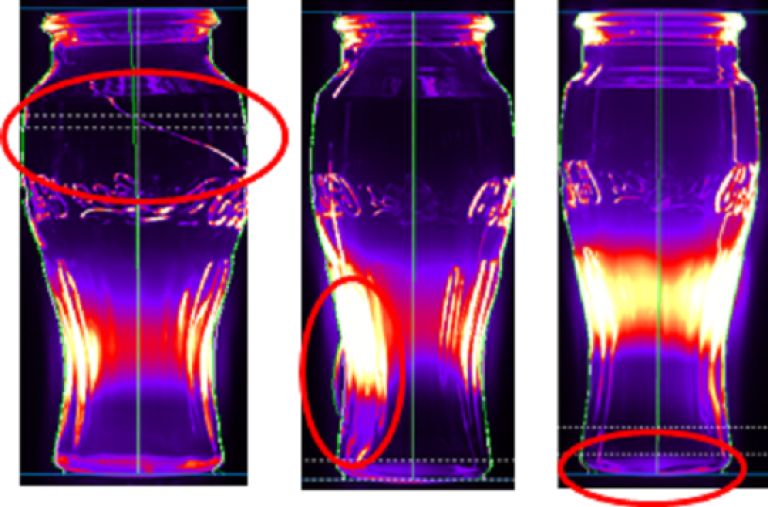
Application and benefits
Typically the tumblers are inspected for similar defects and misshapes (like dents, bulges, fins and eccentricity) as with container glass production. Within the tableware environment this is proven to be especially effective before the cutting machine where the finish part is detached to create the smooth and even rim of drinking glasses.
When avoiding misshaped ware entering into the cutting machine, breakage of glasses and unwanted stoppage of the cutting machine is prevented, raising the efficiency of the production line with over 5%.
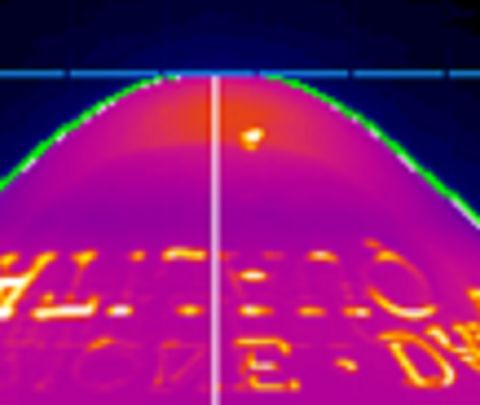
Besides the detection and rejection of critical defects like bird swing, fins, thin walls and stones are detected early in the process, even aspect defects such as stains and black spots are made visible with a special IR-filtration technology. Eliminating these defects before visual inspection after the annealing lehr reduces the risk of providing sub-standard product to the customer. In addition the detection of defects and variations in wall thickness provides valuable process information in real time for the operator to adjust the forming machine setup for early correction.
Automated gob weight control
In addition to the IR-D system, XPAR Vision has also applied the IGC system to the tableware industry to allow automatic and closed loop control of the weight of the gob. With gobs not being visible for optical cameras because views are blocked by the press-blow machine, the XPAR Vision solution to control the gob weight is based on the IR-measurements in the glasses on the conveyor belt. This principle, proven in container glass application, reduces variation of gob weight to less than 0.5% of product weight as shown in the screenshot on the right.
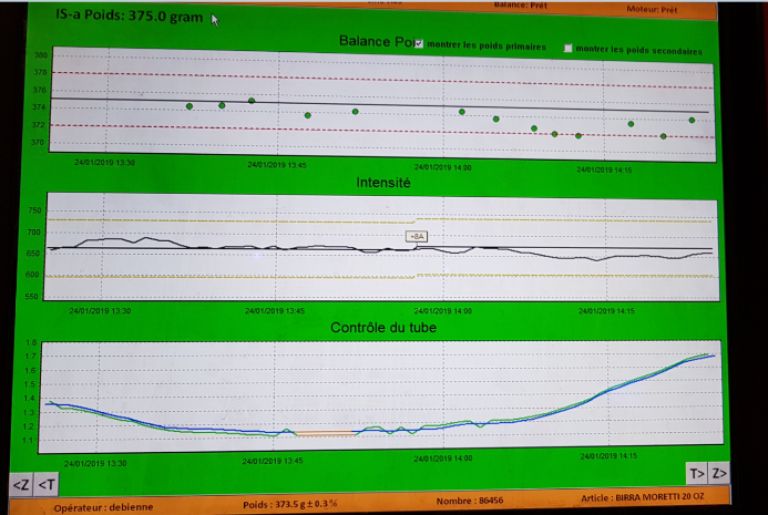
The IGC system automatically regulates the tube height in the feeder without intervention from the operator. With both IR-D and IGC in place, the operator can focus on optimizing the performance of the forming machine, rather than paying attention to unwanted events because of weight variation and product anomalies.
In summary, applying hot end technologies from XPAR Vision in tableware production results in fast payback and opens the door for higher efficiencies by increasing the focus from operators on further process improvements.
For information about IR-D and IGC in tableware production, please contact your Account Manager via sales@xparvision.com or by telephone on +31-50 316 2888.