In every container glass factory held ware and resorting is a pain in the butt, and even getting worse. With XPAR Vision’s Long Term Image Storage this held ware and resorting will be dramatically reduced.
Held ware
In case of any suspicion for bad quality and / or critical defects, pallets of bottles or jars are set aside for the purpose of re-inspection. In the majority of cases this re-inspection is done by manual unloading pallets at the cold end, re-inspecting all containers and then palletizing again. This process of resorting is costly, inefficient, and disruptive for the normal production process as well. As a result, resorting activities are often postponed to “a better moment”, which then leads to a higher number of blocked pallets. Held ware is a huge driver of increased costs. A high number of blocked pallets take up valuable warehouse space, hold captive packaging material (pallets, tier sheets, etc.), put on time customer deliveries at risk, and increase employee headcount.
While held ware is a major KPI in glass factories, all of the costs associated with held ware do not directly show up in factories’ major metrics, and are easily “forgotten”. Furthermore, it is not uncommon that when held ware continues to increase and reaches unmanageable levels, the only feasible options remaining are even more costly; dumping and scrapping of the ware.
Long Term Image Storage (LTIS)
With LTIS all images of all individual containers are stored, including images of both good and rejected containers. Upon the choice of the customer storage can be organized on local hard disks or in the Cloud, for as long as the customer wants. Through the technology chosen literally an “unlimited” number of images can be stored. Logically with the help of an XPAR Viewer the stored images are easy to retrieve, and data is easy to analyze. Images are presented in a grey scale or color.
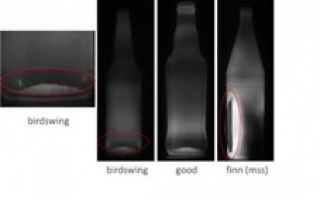
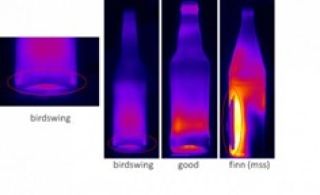
Digital resorting
The basic principle of LTIS is that images can be reviewed at all times, allowing the ability to go back and verify if and when bad quality or critical defects have been produced, and on which cavity or section. As a result, related pallets can be identified precisely, while preventing critical defects from being sent to the customer. Basically by use of LTIS, the inefficient and costly physical resorting is to a great extend replaced by a digital resorting.
In case of internal traceability, the availability of all images including their time stamps allow for accurate determination of minimum quantities of held ware and thus costs of resorting. As such and following the feedback of LTIS users, the held ware and resorting is dramatically reduced. Additionally based in the findings any systems settings of the XPAR IRDs can be improved.
In case of external traceability, the availability of all images including their time stamps allow for precise identification of contaminated pallets, with proof towards the users of glass containers. As such, potential damage (customer complaints, financial claims, recalls, reputational damage) can be managed and limited.
For further detailed information about LTIS please contact sales@xparvision.com.