Loading of the gob into the blank mould is an important sub process in the production of glass containers. Many forming specialists will agree that 70-90% of the critical defects are due to a bad gob loading. Bad gob loading is also a main cause for section stops.
Our Gob Assist monitors the speed, length, position, shape, orientation, time of arrival and trajectory of the gobs falling into the blank moulds, without coming in contact with them. With this information it is possible to easily find and maintain the optimal gob loading and to retrieve optimal gob loading after equipment or job change.
The advantages which in the meantime have been confirmed by customer trials are numerous:
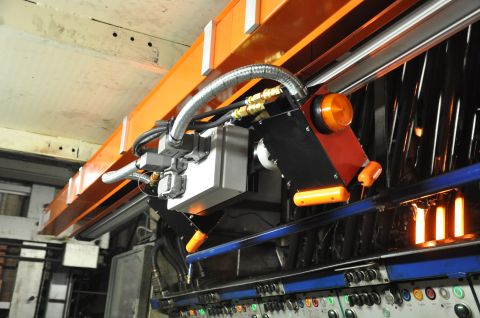
- decrease of downtime: downtime decreases, mainly due to less blockages of cavities due to bad loading, but also due to less changes of blank moulds, deflectors and troughs
- increase of efficiency & productivity: efficiency increases due to e.g. reduction of swabbing cycles, increased lifetime of moulds, deflectors and troughs, decrease of oil usage and optimized coating
- improved quality of output: good loading decreases the number of related defects as glass distribution (thin glass), visual defects, stucked bottoms, freaks and/or deformations of body
- increase of job change performance: good gob loading leads to an increased job change performance due to a reduction of variations over sections (by defining guidelines for time of arrival, dimensions, speed and position and by using availability of reference data from the former run), due to a sustainable set up of the delivery system (height, x/y position, etc.) and due to the knowledge of the influence of cleaning, material changes, etc.
Striking is the insight in the gob loading process of one of our customers. During a few weeks the gob loading performance of a “well organized” production line (nnpb, beer, light weight, high speed) was monitored. In the diagram the position (left) and speed (right) of gob loading is shown during a two week production period.
Immediately one can see the hugh variation of position and speed during loading (position deviation in a range of 10 (!) mm). Looking at these aspects of loading one would conclude that the loading process is totally out of control. Nevertheless, this is where the industry is today. Realizing that with the Gob Assist we will be able to bring these variations down (position less than 2 mm) one should conclude that enormous gains are within reach. Obvious should be the potential for (ultra) light weight: an always accurate position of loading means (very) low variation in glass (thickness) distribution which is a precondition for (ultra) light weight.
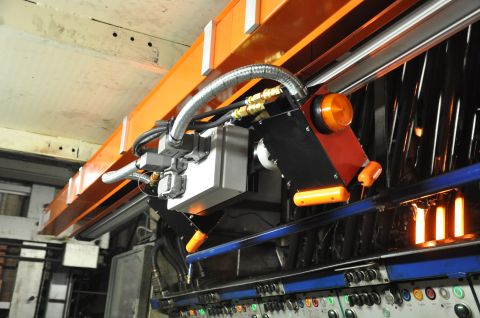