During the recent Glasstec in Dusseldorf, XPAR Vision celebrated its 10th Glasstec anniversary.
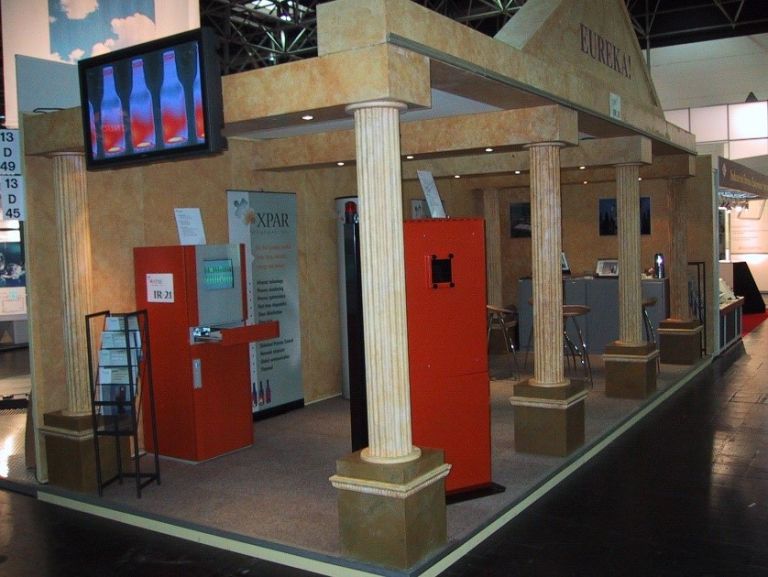
In Glasstec of the year 2000 XPAR Vision started to promote the IR-21 system: InfraRed (the technology used) and 21st century (indicating the start of a new era). The IR-21 was the first successful application for hot end forming process monitoring for the global container glass industry. In 2003 the IR-21 system was succeeded by the Polysigma InfraRed Single camera system. Besides hardware improvements software modules for extensive defect detection were added. In 2007 the Polysigma was succeeded by the Infrared Dual camera system (2007). Two cameras instead of one camera did improve the system capabilities drastically.
Parallel to these changes throughout the years and in close contact with system users world-wide the software has been developed continuously. Today the software enables automatic set up, inspection and forming process monitoring and improvement and also automation (closed loops to IS timing, e.g. ware spacing control, vertical glass distribution control). Besides that, the software enables long-term storage of all images collected, allowing for very effective track and trace.
In the last 20 years, XPAR Vision has developed from a newcomer with a single product (Infrared camera system) for a single industry (container glass industry) into a mature company with a portfolio of sensors and robotics for both container glass and table ware productions. Today, XPAR Vision is world technology leader in its field, with an installed base of far over 600 production lines and with a focus on the hot end inspection & process monitoring, process improvement, quality control and closed loop automation.
XPAR Vision focusses strongly on the development of hot end sensors and robotics. Half of our 30+ staff is dedicated developer. Day by day these developers are working on improving existing solutions and developing new ones, using their backgrounds in Applied Physics, Mathematics, Artificial Intelligence and Computer Science. Together with the Field Service Engineers for technical installation on customer sites and continuous remote support and the Consultants for on-site and remote after sales and implementation support the XPAR Vision team has focus on its customers and the implementation success of its solutions.
“Our motto is “HEading for Perfection”, says CEO Paul Schreuders. “All our staff, without exception, is simply living that, day by day. Our customers say that we have the best support organisation in the industry. That is a compliment. No need to say that I am very proud and extremely happy with our team and all its members”.
During Glasstec 2018 the complete product portfolio was promoted: the IR dual camera system and its newest software, the InfraRed Gob weight Control solution (automatic gob weight control), the GobAssist/BTC solution (monitoring gob loading and temperature parameters including automatic blank and plunger temperature control), the Gob Monitor (monitoring gob shape and temperature profiles at the gob cut) and the revolutionary BlankRobot.
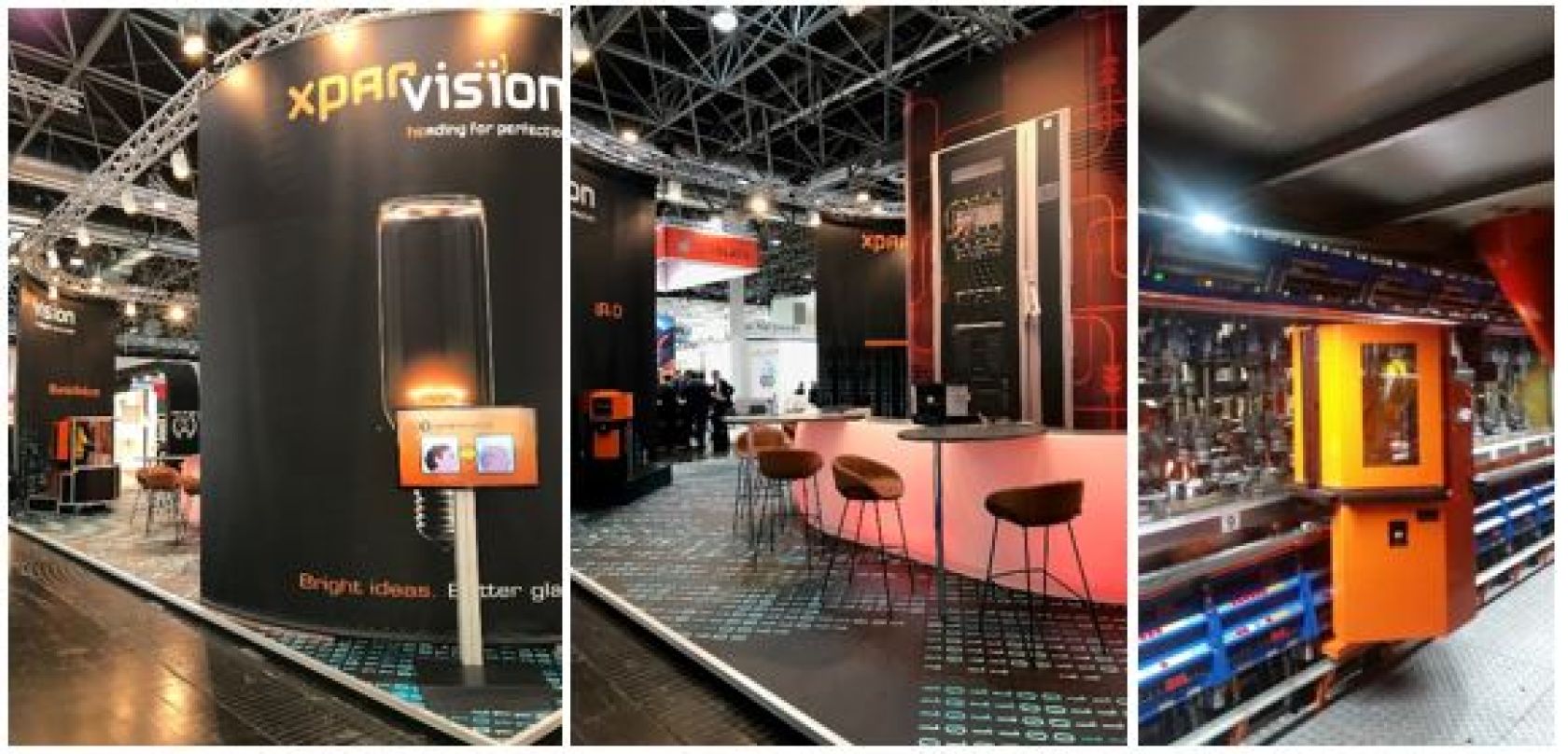
As the name already indicates, our BlankRobot is designed not only for swabbing, but for other applications as well. For blank mould swabbing, XPAR Vision has entered into an exclusive co-operation with LubriGlass Germany. By applying a special LubriGlass lubricant extremely precisely, the swabbing frequency is reduced to one time per three hours only (!). With the BlankRobot the use of lubricant is reduced from 100% by manual swabbing to only 2% (!). Furthermore and most importantly there is only very limited disturbance of the glass forming process: as a result of which the hot end sensors will see other process disturbances much better, like changing glass conditioning, mould wear and ambient temperature. This improvement of measurements will lead to very effective feedback loops and logically has huge impact on the effectiveness of forming process automation.
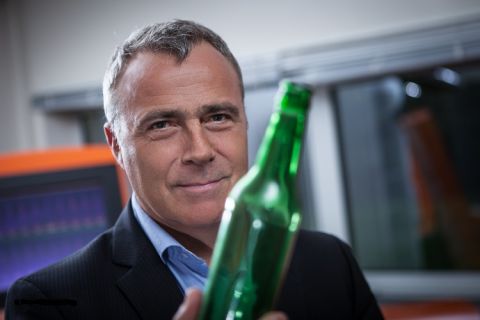
“It is our aim to create a new world for container glass and table ware producers, says CEO Paul Schreuders. “It is in our genes to always aim for that next step, for things that do next exist yet. We strongly believe that with our new technologies we can make glass products lighter and stronger, allowing them to be produced with (almost) zero defects at higher speed and with minimum human dependency. That is our mission and that is what we are working on, all together, with a lot of enthusiasm”.
“Although business reality is not always that easy, we are very proud of the achievements so far. However, looking forward is even more exciting! The close cooperation with many of our customers is feeding the process of continuous innovations. With additional robot functions, integration of hot end sensor data, integration of hot end and cold end sensor data and smart or artificial intelligence, we will make life easier for every glass maker and make glass the preferred and best material choice. For a better world”.