Twenty years ago XPAR Vision from The Netherlands made its first steps into the global container glass industry, being the first introducing Infrared sensor technology for hot end inspection and process monitoring. Since the company has grown into the specialist and technology leader for hot end sensor and robot technology, with the overall ambition of assisting the global container glass industry making its bottles and jars lighter and stronger, produced with zero defects at higher speed.
During the last few years this ambition is more and more supported by a mega trend against plastics and environmental pollution and by clear requests from major breweries and other glass packaging users to drastically reduce the carbon footprint of the packaging materials. Besides and even more important for individual glass makers, following the ambition of lighter and stronger produced with zero defects at higher speed simply pays off.
In this article step by step we’ll give ingredients for realizing this ambition.
Hot end forming: quality focus
Since long hot end forming was steered towards putting as many as possible bottles into the lehr, without too much attention for their quality. Quality was a concern of the cold end. Hot end and cold end, naturally divided by the lehr and the lehr time, like two different worlds. Consequently and in case of quality issues, there was hardly any communication or feedback from cold end to hot end, and if there was any communication or feedback, the time delay due to lehr time made it not too effective. Due to this and in order to ensure good qualities to be sent to fillers, in any cold end area or warehouse one finds a lot of pallets to be resorted.
Quality is made in the hot end. Today good tools are available to actually support a proper quality focus in the hot end.
Use of sensors
Nowadays sensors see more and better and foremost sensors deliver more consistent information than humans. And consistency of information is highly important! Looking at a forming process today many disturbances are affecting the glass making process. Think about cullet quality, viscosity, temperature, glass homogeneity, ambient temperature, deterioration and wear of material and even swabbing, job change, stop/start sections or bottle design. Logically any glass maker aims to minimize the effect of these sometimes unpredictable disturbances on gob condition (weight, temperature, shape), gob loading (speed, length, time of arrival, position), temperatures (parison, moulds, plunger, neck ring) and consequently quality of bottles. Timely, consistent and accurate information about gob condition, gob loading, temperatures and quality of bottles is the starting point for realizing the ambition of lighter and stronger produced with zero defects at higher speed. For the past 15 years numerous (hot end) sensors have become available.
Using sensor information as a starting point creates a world in which facts prevail over opinions. Effectively this means that less valuable time is lost on opinions and more valuable time can be spent on solutions.
Inspection versus process monitoring
With todays’ hot end sensors for bottle monitoring critical defects can be eliminated at the hot end. Logically implementing these devices are of help in improving the quality to customer. Nevertheless, a hot end sensor for bottle monitoring should not be used of inspection only. The reasons are obvious. First, all existing hot end sensors for bottle monitoring are able to inspect many but not all types of defects. Moreover, like any inspection machine (in hot end or cold end) no sensor will be able to be 100% effective for inspection. And last but not least, as every rejected bottle or jar is a direct loss of production time and energy (CO2), the focus should be on preventing defects to be produced.
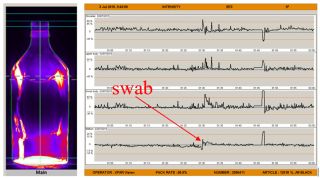
The main purpose of having a hot end sensor for bottle monitoring is the fact that inspection of single bottles according to customer specifications, despite not being 100% effective, eliminates critical defects but moreover allows for collecting signals which give a good indication for cavity-, section-, front or back gob- or machine-performance. Eliminating critical defects including stuck and fallen ware in the hot end ensures a smooth flow through the coating hood and cold end inspection equipment. The indication for cavity-, section-, front or back gob- or machine-performance allows for effective root cause analyses (learning, preventing) and fast remedial action in case of problems. Fast remedial action in the hot end on the bases of in real time information does directly lead to improvement of efficiency, and is the starting point for stabilizing the forming process. In figure 1 and example is given.
Lowering disturbances
As being said many disturbances (cullet quality, viscosity, temperature, glass homogeneity, ambient temperature, deterioration and wear of material and even swabbing, job change, stop/start sections or bottle design) are affecting the glass making process. Basically these disturbances are root causes for forming process variations, and the higher the level of forming process variations the more defects are produced. It speaks for itself that lowering the level and frequency of disturbances will be of great help in realizing the ambition of lighter and stronger produced with zero defects and higher speed.
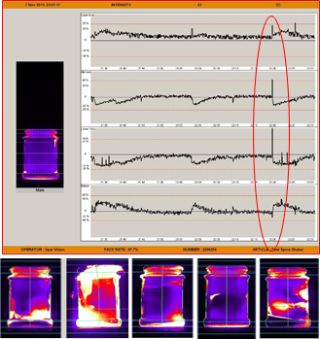
An example. Currently there is a lot of emphasis on swabbing. It is true that swabbing is one of the main disturbances in the glass making process. In figure 2 an example is given. It is a remedy on one site, but an enemy on the other side. In lowering the disturbances due to swabbing one could take different routes:
a. Organizing manual swabbing; strongly implemented SOP’s whilst monitoring the effect of each swabbing cycle
b. Automating manual swabbing by use of automated lubrication systems; automated swabbing in comparison to manual swabbing ensures consistency in frequency and impact
c. Minimizing swabbing by use of automated lubrication system; minimizing swabbing in comparison to automated swabbing with focus on reducing frequency and impact
The reduction of the disturbances due to swabbing goes from a to b to c. Option C has the lowest disturbance. XPAR Vision’s newest BlankRobot fits this option, which due to the focus on reducing frequency and impact, allows for other functions to be executed by the BlankRobot. Logically it is up to the glass maker to make choices here.
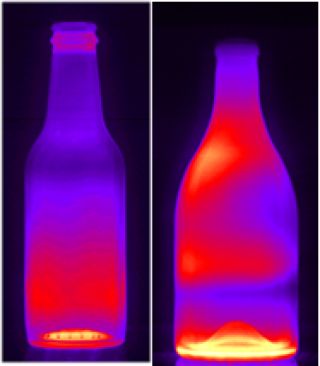
Managing process variations: even glass wall thickness variation
Today in order to compensate for the relatively high level of process variations due to the disturbances as mentioned, we simply use more glass. In order to meet the customer’s specification of 1mm whilst achieving a reasonable level of efficiency, a design specification will range from around 1.7mm (nnpb) up to sometimes more than 2.5mm (bb).
This oversizing is performed on purpose and in order to avoid the risk of producing faulty bottles; in earlier days, when they were unable to make strength calculations, this was the way to construct buildings that would last for centuries. This oversizing compensates for high level of process variations (or the low level of forming process control) and is generally accepted by glass container manufacturers and their customers.
As a result no single bottle is the same. Monitored by an infrared sensor at the hot end we clearly can see that forming process variation leads to bottle variation in terms of wall thickness variation (glass distribution). This glass distribution basically has two components: vertical glass distribution and horizontal glass distribution. In figure 3 an example is shown of vertical and horizontal glass distribution.
Reviewing many bottles produced we can see a continuous shift in glass distribution, both vertically and horizontally. In order to reduce weight of bottles and to prevent defects from being produced, we should prevent these shifts from happening. Controlling the glass distribution is the key to lighter and stronger bottles and jars, produced with (almost) zero defects at higher speed. Logically controlling the glass distribution does require continuous monitoring of bottles and jars produced, and measuring everything we do against changes in glass distribution. In order to effectively manage the forming process glass distribution is THE reference.
Combining and analyzing data: creating intelligence
Using more and more sensors leads to more and more data. Smartly combining and analyzing these data potentially gives more and better information for sake of more effectively managing process variations.
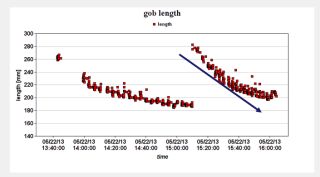
Ultimately we have a dream: one big database with all data available, automatically combined in a machine learning type of environment, creating most effective closed loop algorithms, etc. Let that be a dream. In our view we need to be more practical. For example, loading data or temperature data relate to bottle data: once we know the relation we will be able to control loading and temperatures in such a way that we produce bottles with less shift in glass distribution and thus less defects. And also, some cold end data (like blisters, cracks, etc.) are a clear indication of a process variation. Even if not noticed in the hot end, using these data helps reducing process variations. In figure 4a, 4b and 4c another example is shown.
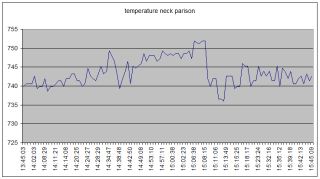
Strong organization: SOP’s or if possible forming process automation
Once sensors are applied, we should organize ourselves around the information provided by the sensor. It does not make any sense having sensors and in the meantime having operators and/or specialist not using the sensor information. As being said, sensors see more and better and foremost sensors deliver more consistent information than humans. And consistency of information is highly important!
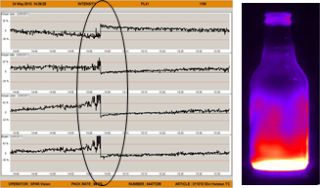
The sensors continuously monitor the status of gob condition (weight, temperature, shape), gob loading (speed, length, time of arrival, position), temperatures (parison, moulds, plunger, neck ring) and consequently quality of bottles. Any change has a cause. Once this caused is known, a Standard Operating Procedure can be set up and applied. Applying SOP’s makes life easier for all. From feedback of our customers we learn that they indeed experience that integrating new employees in the hot end is becoming much easier due to the use of sensors and SOP’s.
Ideally and especially when machines are becoming bigger (which operator can control 48 cavities?), when possible automation should be applied. In this context, the sensor observes, analyses and through feedback to the IS timing, the necessary adjustments are made. As the feedback is computer feedback, adjustments can be made within milliseconds. Even the very best operator/specialist will never be able to do this.
Within the past five years, (hot end) automated control loops have become available for controlling gob weight, ware spacing, mould temperature, plunger process and vertical glass distribution. It is to be expected that in the near future, more control loops will become available. Experience shows that all different control loops once applied basically have the same positive effect; the process variation is reduced and the bottles show less shift in glass distribution and have less defects.
Pay off
Although may be not always too precise (*) in this article ingredients are given for realizing the ambition of lighter and stronger produced with zero defects at higher speed. As container glass industry members we need to embrace this ambition now, utilizing the mega trend against plastics and environmental pollution and following the clear requests from major breweries and other glass packaging users to drastically reduce the carbon footprint of the packaging materials. Besides and even more important for individual glass makers, following the ambition of lighter and stronger, (almost) zero defects at higher speed simply pays off.
Personally I am convinced that we as container glass industry can do up to 25% better than today. This 25% relates to less weight, less defects, higher speed. In addition, following the ingredients as mentioned in this article, it’ll help us to cope with a workforce which is ageing, the difficulty of hiring, integrating and retaining new employees and health and safety issues which will become more and more relevant for all of us.
(*) feel free to contact us to discuss about this subject and the tools that are available for hot end forming process optimization