Following his views on optimising forming process stability and reducing the weight of glass in general terms (Glass Worldwide issue 74), from issue 75 onwards Paul Schreuders explores the different (individual) steps to be taken towards optimising forming process stability and reducing the weight of glass containers. Here, the focus is on various blow side disturbances that have not yet been touched by former issues and how XPAR Vision’s solutions can be of help.
As explained in issue 74, following the Paris Climate Change Conference (COP21) and taking their social responsibility seriously, many if not all food and beverage packing companies are actively working to reduce their carbon footprint. Since packaging is a substantial part of this carbon footprint, supply chain collaboration is a key for success. Knowing the competitive field of metal, plastics and bio-based packaging, for glass the keys to survival are to recycle and reduce weight (improving the content-to-glass ratio). Reducing weight requires further optimisation of forming process stability.
Last step in forming a glass container
In previous articles in the Amazing discoveries series, it has been explained that instability of gob weight, gob temperatures, gob homogeneity, gob loading and parison design, as well as process disturbances influence parison forming. Each forming step results in a characteristic in the infrared footprint of the final product that is identified by the IR-D system. After all process steps at the blank side have been reviewed by means of infrared characteristics, this the final article of this series concentrates on the ultimate step in the creation of a glass container: Final forming. Again, final forming will also create characteristic infrared influences that can be derived from infrared data and images.
Final forming
During final forming, most energy (70%-75%) has to be extracted from the glass. Blow mould cooling, blow mould material, blow head, final forming time, dead plate and conveyor belt cooling are the main factors that extract energy from the parison to create a container to meet customer specifications. Obviously, this heat exchange requires time to come into effect.
Final forming highly influences the speed at which glass containers can be produced. As everyone knows, speed of production is one of the most important factors in the profitability of a production line. In this respect, it is necessary to consider that certain geometrics like verticality and ovality are negatively influenced when speed is increased. Besides the importance of production speed final forming is also the process step where many critical defects are created, eg sharp fins, pinched neck, birdswings or freaks (figure 1).
Here, as a process information and critical defect detection tool, the IR-D becomes indispensable. All influencing aspects mentioned above can be made visible by the IR-D system. Every change in these aspects is translated into the infrared intensity levels and anomalies in quality or dimensions are detected.
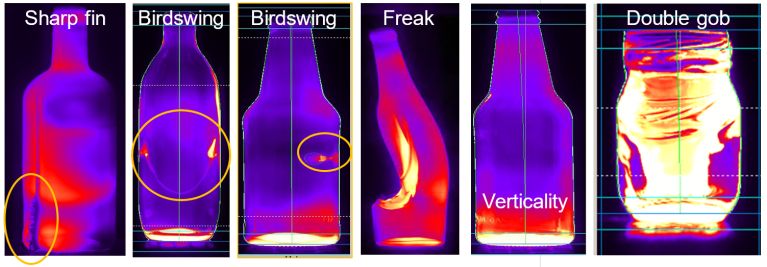
Defects appearing at final forming
Rejected defects in IR-D are supported by control charts showing the historical process performance for the particular cavity. These control charts often contain crucial information that explain the root cause of a defect.
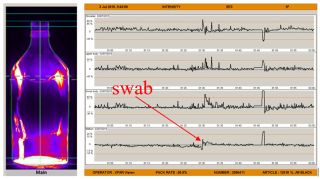
Figure 2 shows the detected birdswing combined with the control chart information. A birdswing could have several causes, where the parison is collapsing at a certain moment in the process due to high overpressure in the blow mould, a too high invert speed or a parison that is too hot. An event in the process results in a critical final form condition for the creation of birdwings. The control chart in figure 2 gives the conclusive answer for the actual event that initiated the changed final form condition.
In most cases, sharp fins (figure 3) are caused by too high invert speed and/or a parison that is too hot, resulting in a swing of the parison into the blow mould with glass become trapped between mould halves. It is often seen that the tolerances in timing setup are too tight, eg the blow mould closes too quickly, leaving no time for the parison to be well positioned inside the blow mould.
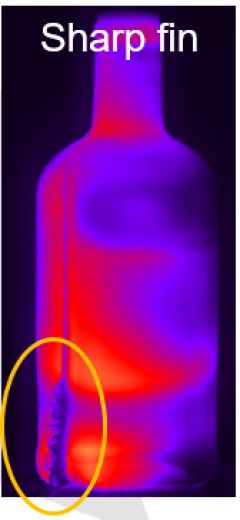
Leaners
Verticality in the glass container or leaners have several possible root causes. To determine whether it is related to shorter blow mould time or insufficient blow mould cooling, poor glass distribution, a bad blow head, poor take-out movement or low dead plate cooling, the IR-D provides information on multiple aspects, allowing a definite root cause determination. From the measurements of verticality values in several locations in the product combined with infrared intensity distribution values, one is able to determine if the root cause has either a thermal or a mechanical origin.
In figure 4, the example is given that the rejected product due to verticality shows in the infrared intensity measurement very high levels in the bottom area of the container. Also, it is clearly visible from the image that deformation starts in the heel area. Combined information concludes that the verticality problem is caused by shifted glass from the neck/shoulder area to the bottom area, a thermal cause.
A mechanical root cause is visualized in following example; the infrared intensity levels are normal indicating no thermal disturbance. The verticality measurements in the body and neck area shows the deformation in the neck area only. This indicates a problem with the take-out movement (figure 5).
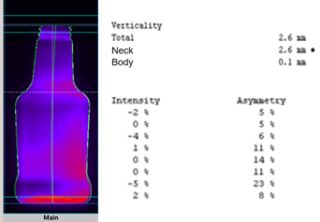
Defective blow head
In the following situation (figure 6), the glassmaker suffered a production issue on one cavity where a verticality problem occurred. Reviewing the infrared intensity chart, the same cavity showed a higher level of average total intensity (red circle).
This higher infrared intensity indicates that the temperature of the product is higher compared to all other cavities. Possible root causes are higher mould temperature (blocked cooling holes) or a poor blow function (leaking hose or poor blow head).
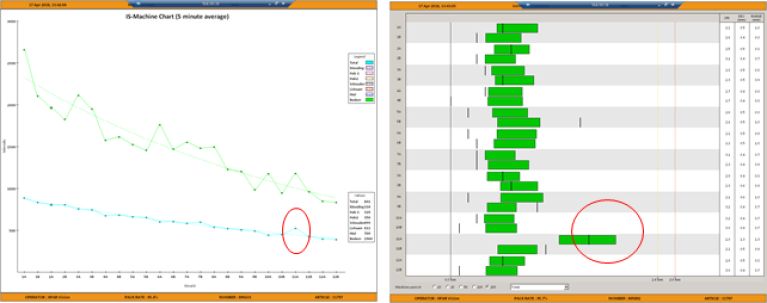
Checking these possible causes resulted in the discovery of the real cause. The blow tube in the blow head was damaged and off-centered as well (figure 7). This minor difference has immediate influence on heat transfer during the final forming process.

Speed
At the blow mould side, it is very important that the heat transfer is optimally adjusted to create products that are dimensionally perfect, without surface defects and cracks. Heat being extracted too strongly will lead to visual surface defects and/or cracks. On the other side, when heat transfer is too low, the product will show dimensional distortions.
As stated earlier, during final forming most energy (70%-75%) has to be extracted from the glass. This implies that control over the heat transfer in the blow side is critical when increasing speed of production. Final forming must be kept stable at a new level as a precondition for successfully speeding up the IS machine. To manage the heat transfer, one can increase cooling, improve the efficiency of cooling or improve blow head design for correct pressure and flow of air.
When increasing speed, the IR-D gives important trend information to follow up on the process of change. Figure 8 gives an example of a trend graph for the average verticality of all cavities. After the speed change, the level of verticality in the products increases. It is important to take timely necessary actions to bring the forming process within limits to continue to meet customers’ quality specifications.
Also, when new and improved equipment is applied (eg a changed blow head design), the trend graphs available in the IR-D system are of great support to determine the effectiveness of an improvement.
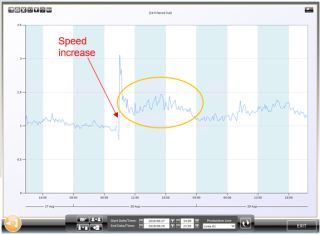
Crucial rejects
Recently, another functionality has been added to the IR-D, the so-called ‘crucial reject’. This function has been specially developed for defects like sharp fins and double jar, freaks that could also shatter small particles of glass at the section when the defect is produced. With the detection of these defects, the reject can be determined as ‘crucial’. The respective container will be rejects by the IR-D combined with an additional action; eg remove all products from that section or even from the entire IS machine to ensure that no product is affected by small glass particles.
Conclusion
In summary, IR-D’s infrared measurements of each glass container unveil many process data and information of process events influencing final forming. Defect detection capabilities of the IR-D combined with the available process information help the user to identify and determine the root cause accordingly. Eliminating root causes is the duty of all glassmakers, rather than masking the symptoms. Only then can step-by-step process improvements be effected. Full use of the IR-D system and given information to optimise process stability is where the most benefits are derived.
It has been explained in ‘Amazing discoveries… 16’ that IR-D infrared information is bringing extra added value in areas other than inspection and process monitoring of running production. Evaluation with infrared information of the forming process leads to process improvements, with important opportunities for companies to increase profitability. Introducing IR-D data/information to departments other than production and quality assurance will be a true eye opener.
Next steps
The scope of this ‘Amazing discoveries’ series of articles is to explore (pre)conditions and steps to be taken towards optimising process stability and reducing the weight-to-volume ratio of glass containers. By monitoring final forming parameters and detecting related critical defects, the IR-D offers great value to improve process stability and increase speed.
Control and stability of the blank side forming process are prerequisites for performance improvement in such areas as reduced product weight to reduce the carbon footprint of glass packaging. This answers the needs of customers of glass container manufacturers (see the first paragraph of this article) to secure or even regain competitiveness against other packaging materials.
This is the last article in the series on applying infrared in the forming process. XPAR Vision will continue with a different series of articles to share knowledge and create awareness of the possibilities today and in the future.
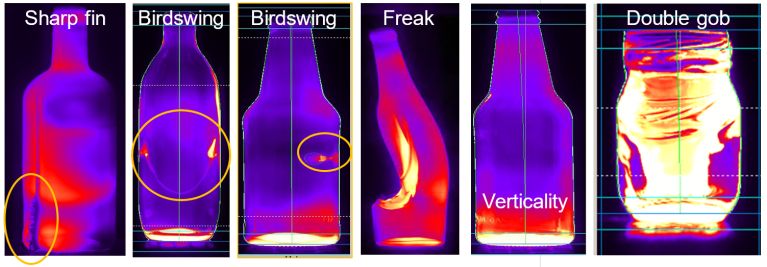