As explained in issue 74, following the Paris Climate Change Conference (COP21) and taking their social responsibility seriously, many if not all food and beverage packing companies are actively working to reduce their carbon footprint. Since packaging is a substantial part of this carbon footprint, supply chain collaboration is a key for success. Knowing the competitive field of metal, plastics and bio-based packaging, for glass the keys to survival are to recycle and reduce weight (improving the content-to-glass ratio). Reducing weight requires further optimisation of forming process stability.
Parison forming
From previous articles in the ‘Amazing discoveries’ series, it has been explained that instability of gob weight, gob temperatures, gob homogeneity and gob loading reflect highly on the parison forming stage. Deviations in the above-listed conditions lead directly to bad parison forming, consequently resulting in poor quality glass containers. Examples of defects that are caused by a badly formed parison are thin bottom, thin neck and blisters.
It is commonly known that forming of the parison in the blanks is crucial to the final quality of a glass container. Equally important is that proper and stable parison forming is key for production efficiency and a crucial pre-condition for implementing speed increases and lightweight glass container production.
With IR-D’s infrared measurements of each container, the effects of changing input conditions in real-time are shown in the parison forming process. Typically, these effects are similar for all forming processes (blow-blow, press-blow and NNPB).
Parison design
So far, one crucial input for the parison forming process is unmentioned. This is the design of the parison or blanks. Even if all of the above-listed input conditions are perfect, a wrong parison design will still lead to serious quality problems with the final product, mostly reflecting in several glass distribution issues.
When a poor parison or blank design is introduced to production, everything possible will be done to compensate for it with IS timing and/or cooling setup, changing gob shape in order to minimise the effect on the quality of the glass container. But by doing so, production keeps compensating with every deviation in the forming process conditions. The result is a fire-fighting situation, where instability of the parison forming process rules the operator’s job.
When testing a new parison design (sampling) the IR-D information of infrared intensity distribution in the final container gives excellent indications of the glass distribution of that container. The IR-D measurements are indispensable for the determination of the quality of the parison design, which becomes visible immediately during sampling. Supported by the IR-D measurements stored in the XMIS database, detailed feedback based on data (factual information) can be given to the Mould Design Department.
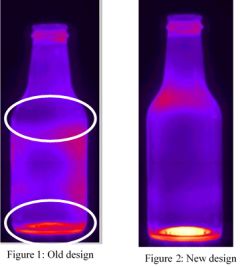
Case study
With the production of a 25cl (165g) beer bottle, the cold end reject rate for thin wall thickness in the shoulder varied from 1% to 5%. The production team changed the IS timing setup to get more glass into the shoulder area. The effect was positive for the wall thickness in the shoulder but resulted in thin bottoms, out of customer specifications (see figure 1).
In finding a good balance in glass distribution, the production team continuously had to make changes to the IS timing and made several mould exchanges to compensate for changing parison forming conditions. This typical firefighting situation resulted in a low average hot end performance and overall efficiency.
When comparing IR-D measurements during sampling of a new blank design, it immediately became obvious that the new design was a big improvement (see figure 2). The infrared intensity distribution (glass distribution) changed for the better; with more glass in the bottom and in the shoulder area, the glass is uniformly distributed.
The impact on quality and efficiency was very positive. With the new parison design, glass distribution problems were minimised and performance increased by 3% to a stable average level. On top of that, the stability created became a precondition to increase the production speed of this beer bottle by 2%! This generated even more profit.
The information of the IR-D delivered valuable input to evaluate the new design and resulted in optimised production performance. With sych gains, the return-on-investment is a no brainer.
Design change evaluation
Besides the parison or blank design evaluation, with the infrared information from the IR-D system effects of other design changes can be measured and evaluated. This includes cooling set-up/cooling design of moulds or plunger design (blow-blow) and volume changes of the blanks during their lifetime due to mould maintenance. Fundamentally, all design changes of equipment that result in thermal influences or glass distribution changes can be measured and monitored by IR-D.
Benefits
In this latest of the ‘Amazing discoveries..’ series of articles, it is emphasised that IR-D infrared information brings extra added value in other areas than only inspection and process monitoring of running production. Evaluation with infrared information of the forming process leads to process improvements, with major opportunities for companies to increase profitability. Introducing IR-D data/information to other departments than only production and quality assurance will be a true eye opener. XPAR Vision’s sales team and consultants are available to discuss opportunities.
Next steps
The scope of this ‘Amazing discoveries’ series of articles is to explore (pre)conditions and steps to be taken towards optimising process stability and reducing the weight-to-volume ratio of glass containers. By monitoring the influencing conditions to the parison forming process and evaluating new parsion designs, the IR-D offers great value. Control and stability of the parison forming are prerequisites for performance improvement in such areas as reduced product weight to reduce the carbon footprint of glass packaging. This answers the needs of customers of glass container manufacturers (see the first paragraph of this article) to secure or even regain competitiveness against other packaging materials.
In the next article of this ‘Amazing discoveries’ series, the author will again describe the blank side of the forming process and then specifically the effects of coating, third party weight control, swabbing etc.
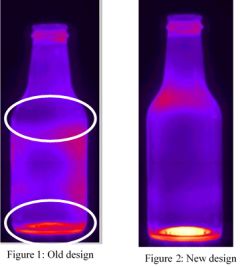