Following his views on optimising forming process stability and reducing the weight of glass in general terms (Glass Worldwide issue 74), from issue 75 onwards Paul Schreuders explores the different (individual) steps to be taken towards optimising forming process stability and reducing the weight of glass containers. Here, the focus is on gob loading and how XPAR Vision’s solutions can help to stabilise thi processs.
As explained in issue 74, following the Paris Climate Change Conference (COP21) and taking their social responsibility seriously, many if not all food and beverage packing companies are actively working to reduce their carbon footprint. Since packaging is a substantial part of this carbon footprint, supply chain collaboration is a key for success. Knowing the competitive field of metal, plastics and bio-based packaging, for glass the keys to survival are to recycle and reduce weight (improving the content-to-glass ratio). Reducing weight requires further optimisation of forming process stability.
Stable gob loading
Gob loading is an important ‘sub-process’ of the glass forming process. Delivery of the gob from gob cut into the blank is a highly uncontrolled process. It incorporates many factors that influence the forming process, eg entering position into the funnel/distributor, friction in delivery because of bad alignment, wear of coating, deflector position, etc. Due to these factors the speed, length, geometrics, time-of-arrival and the loading position of the gob are compromised, resulting in bad loading into the blanks.
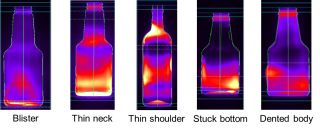
The importance of stable gob loading over time is obvious. When the gob loading condition starts to deviate from normal, it will influence the stability of the forming process directly. Needless to say, it affects the quality of the container produced. Variations in loading immediately leads to variations in glass distribution in the container and to critical defects accordingly (see examples in figure 1).
Gob loading monitoring
In order to create this stability in gob loading, one must understand where the deviations originate. A precondition is to create consistent gobs at the gob cut. When this consistency is given, the gob enters the delivery system by which the gob is forwarded to and ultimately enters the blank.
Because of the design of the IS machine, the trajectory of gobs between each section or even each cavity is different. Here, the variation is already a given factor. The different lengths of trajectories (inner versus outer sections) result in less or more friction the gobs encounter, resulting in changed gob geometrics (see figure 2a*).
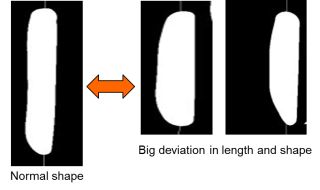
Even odd shaped gobs will leave the delivery, like the example in figure 2b*. These examples of gob deviation are not recognised by eye but at the same time lead to defects in the container. Logically, due to changed geometrics and related changes in speed and time of arrival, these deviations will influence the amount of friction the gob will meet when it enters the blank mould. The higher friction it encounters, the more impact there will be on the forming process. This will result in defects or even blocked sections.
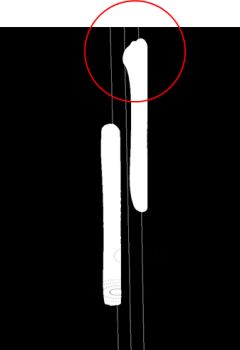
Gob loading control
Traditionally, the influencing factors are controlled by eye and extensive practical experience is required to take the proper remedial actions. However, the human eye is physically restricted to analyse the details due to the speed of the gob (approximately 7m/sec). As a result, different people will make different analyses by their personal observations. Consequently, each person will make different corrective actions to a same loading situation.
With no information or even warnings from a measuring system like IR-D, the typical behaviour of an operator to solve problems in the forming process is to swab the blank mould. As the root cause is not visualised to the operator, he or she will not work on solving the real cause. The effect is only temporary and the problems will reoccur at some time. Without IR-D and/or GobAssist, the operator cannot analyse the problems and/or define the root cause. The problem solving method applied is restricted to trial-and-error, resulting in losses of bad containers and instability of the section and machine performance. This behaviour is shown in figure 3, illustrating the necessity for making decisions based on factual measurements!
When certain factors like the position, length or shape of the gob deviate too much, it will have an impact on the forming process at the blank side: The IR-D will show in the data the change in the process and ultimately, if no timely remedial action is taken, it will detect and reject bad quality containers.
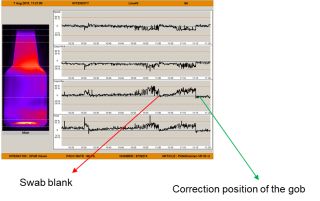
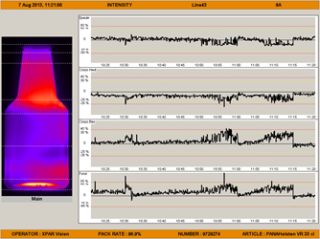
The control charts for the particular cavity, shown by IR-D, gives information that loading is changing. This can be supported by warnings that the system can generate on the user interface screen. Referring again to the same IR characteristic, a typical situation for the NNPB forming process, gob length is getting shorter due to more friction in the deflector. The IR intensity in the bottom/heel increases and the intensity in the neck/shoulder will decrease (see figure 4).
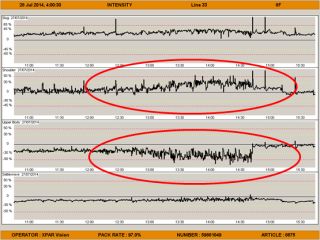
While the gob became thicker (a logical consequence when length gets shorter) it met more friction when loading into the blank mould and the glass will not enter as deep as normal and the pressing process changes glass distribution.
Also, with the blow-and-blow process, deviated loading conditions will be visualised by IR intensity changes in several areas of the glass container. More variation in IR intensity measurements are clear indicators that the root cause comes from gob loading (see figure 5a). In the IR-D system software, a recently developed warning feature has been introduced to visualise for increased variation levels of IR intensity in the overview screen of the user interface (see figure 5b). This warning indicates to the operator to check the gob loading of the cavity when a set threshold is exceeded. Proper and consequent use of this option by good instructions (eg standard operating procedure for the operator) will prevent defects being produced due to bad loading.
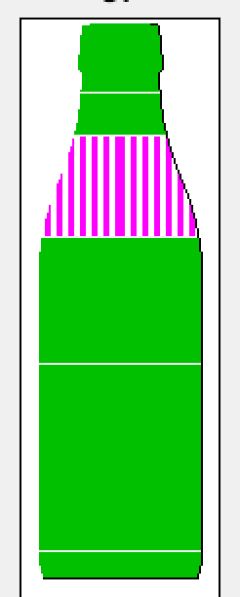
Next steps
The scope of this Amazing Discoveries series of articles is to explore (pre)conditions and steps to be taken towards optimising process stability and reducing the weight-to-volume ratio of glass containers. By stabilising loading of the gob by means of automatic (system) control, another pre-condition is met. This leads to less variation and thus stability of the container forming process. Control and stability are prerequisites for performance improvement in such areas as reduced product weight to reduce the carbon footprint of glass packaging. This answers the needs of customers of glass container manufacturers (see the first paragraph of this article) to secure or even regain competitiveness against other packaging materials.
In future articles of the Amazing Discoveries series, the author will describe the next phase in the forming process, (blank) mould design, where optimisation of process stability can be realised.
Benefits
It is obvious that with the correct use of infrared sensor systems and dedicated gob monitoring system*, the gob condition in all its aspects can be controlled. Early or even real-time signals are presented to the IS machine operator to act upon. With these tools, stable gob loading can be achieved without trial-and-error actions of operators. This results in less variation in the forming process and a reduction of (critical) defects produced.
In more and more areas, direct steering (closed loop automation) is in place or will become available shortly. XPAR Vision is working actively to bring sensor solutions to the market or facilitates IS and other suppliers to develop in this respect.
* All images taken by XPAR Vision GobAssist. The GobAssist tool is on near a real-time basis taking measurements of the speed, length, shape and diameter of the gob. Any deviations from the defined tolerances are seen by warnings of the system. For the IS machine operator, it is easy to interpret and immediate remedial actions can be performed by him or her. For further details on GobAssist, refer to the Amazing Discoveries series in 2017.
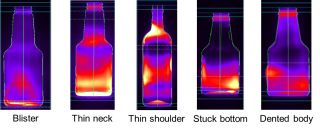