Twenty years ago, Netherlands-based XPAR Vision made its first steps into the global glass container industry, the first to introduce infrared sensor technology for hot end inspection and process monitoring. Subsequently, the company has become a specialist and market leader for hot end sensor and robot technology, with the overall ambition of assisting the global glass container industry to make its bottles and jars lighter and stronger, produced with zero defects and at higher speed.
During the last few years this ambition has become more and more relevant for container glass producers as they are confronted with the following challenges:
- Competition against other packaging materials and request from major fillers to reduce the carbon footprint, thus driving productivity improvement and weight reduction;
- Legal requirements from (national) governments regarding health and safety;
- Attractiveness for new generations, knowing existing working conditions and ambitions from the millenniums, in other words how to maintain a good workforce;
- Changing customer requirements which put pressure on becoming more flexible whilst dealing with more complexity
The answer to all these questions is to change traditional ways of operating IS machines: from mainly manual interpretation and control by humans to mainly machine interpretation and control by sensors, robots, data, artificial intelligence and automation. By doing so a step wise change in the level of forming process control will become feasible, whilst given an answer to all challenges mentioned.
The level of forming process control
Looking at a forming process today many disturbances are affecting the glass making process. Think about cullet quality, viscosity, temperature, glass homogeneity, ambient temperature, deterioration and wear of material and even swabbing, job change, stop/start sections or bottle design.
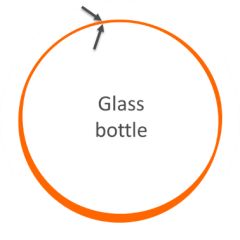
In the world of container glass forming with mainly manual interpretation and control, these disturbances lead to relatively high variations in the glass forming process. These high variations in the glass forming process result in bottles with variations in glass distribution or glass wall thickness, both vertically and laterally, of more than 50% (!). In the meantime efficiency levels (pack to melt) are in the range of 85-90%, which basically means that 10-15 out of 100 gobs cut do not result in a good bottle or jar (defects produced are 10-15%). In the knowledge that the majority of defects produced originate in the variation of the glass forming process, variations in glass distribution or glass wall thickness also produced defects (figure 1). They are a main indicator for variations in the glass forming process and thus, for the level of forming process control.
A step wise change, but not overnight
With mainly machine interpretation and control by sensors, robots, data, artificial intelligence and automation, a step wise change in the level of forming process control will become feasible.
Simply think of differences between the two worlds of container glass forming: the old world with mainly manual interpretation and control by humans or the new world with mainly machine interpretation and control by sensors, robots, data, artificial intelligence and automation. E.g.
- humans have different eyes and experiences, thus see things differently and certainly not consistent
- humans due to other tasks to execute can only review and check about 100 bottles in one hour, whereas production speed nowadays is up to 40.000 bottles in one hour; sensors can see every single bottle
- humans can’t be as accurate and consistent as sensors or robots: humans can’t discriminate mm length differences of falling gobs (7 meters/second), whilst these differences have effect on quality of bottles, and swabbing by humans in comparison to swabbing by robots is much less consistent and leads to much more forming process disturbances, and thus variations, and thus defects
- issues on any IS machine can be many and cavity related, machine related, section related, or related to only front or only back gob; how can any human continuously and accurately review 48 (12 x 4 or 16 x 3) cavities?
Knowing these differences it is not difficult to understand that in the new world one is able to create a step wise change in the level of forming process control. Of course this step wise change will not happen overnight. Step by step one moves from more experienced base to more science based, and from more manual control to more automatic control. And yes, this new environment for sure is more attractive for millenniums, and due to a higher level of automation health and safety is becoming less of a burden, and flexibility and complexity are better taken care of. But most importantly this “new” forming process creates bottles and jars with much less glass wall thickness variations and much higher efficiency levels. Lighter and stronger containers, produced with much less defects at higher speed and less human dependency are the result.
25% improvement is possible!
Knowing the values of the indicators for the variations in the glass forming process, namely variations in glass wall thickness of more than 50% and defects produced of in between 10 and 15% there is a lot of room for improvement. Based on 20+ years of experience in the field of forming process, and based upon an unlimited number of good examples, I dare to state that in the new world of container glass forming, with the right tools, focus and ambition, the container glass industry is able to do 25% better then today! This 25% is mainly coming from efficiency increase, weight reduction and speed increase and equalizes a value of in between Euro 3.5 M and 7 M per production line per year! And due to the origin (energy, materials, capacities), everybody benefit: container glass manufacturers, container glass users and last but not least our planet!
Creating the new world of container glass forming, a recipe for change
Within this chapter a recipe for change will be given.
Hot end forming: quality focus
For a long time hot end forming was steered towards putting as many as possible bottles into the lehr, without too much attention for their quality. Quality was a concern of the cold end. Hot end and cold end, naturally divided by the lehr and the lehr time, were like two different worlds. Consequently and in case of quality issues, there was hardly any communication or feedback from cold end to hot end, and if there was any communication or feedback, the time delay due to lehr time made it not too effective. Due to this and in order to ensure good qualities to be sent to fillers, in any cold end area or warehouse one finds a lot of pallets to be resorted.
In order to create the new world of glass forming one should admit that quality is made in the hot end, and organize accordingly. Tools are available to actually support a proper quality focus in the hot end.
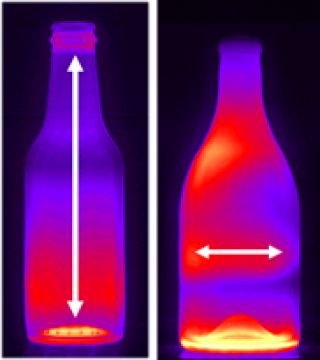
Use of IR sensors
The glass forming process is determined mainly by temperatures and exchange of hear. The result is a bottle or jar with a certain glass distribution. As Infrared (IR) measures the thermal properties and the glass distribution of the just formed container, IR is the best sensor for hot end bottle inspection.
By applying IR sensors critical defects can be eliminated at the hot end (figure 2). Logically, implementing these devices is of help in improving the quality to delivered to customers. Nevertheless, hot end sensors for bottle monitoring should not be used for inspection only. The reasons are obvious. First, these sensors are able to inspect many but not all types of defects. Moreover, like any inspection machine (in hot end or cold end) no sensor will be able to be 100% effective for inspection. And last but not least, as every rejected bottle or jar is a direct loss of production time and energy, the focus should be on preventing defects to be produced.
Reviewing all bottles produced allows for collecting signals: besides defects one can see shifts in glass distribution, both vertically and laterally, changes in verticality and shape of bottles, etc. As these signals can be related to the cavity of origin, analyses can be converted in indications for cavity-, section-, front or back gob- or machine-performance. These indications allow for effective root cause analyses (learning, preventing) and fast remedial action in case of problems. Fast remedial action in the hot end on the bases of in real time information does directly lead to improvement of efficiency, and is the starting point for improving the level of forming process control. An example is given in figure 3.
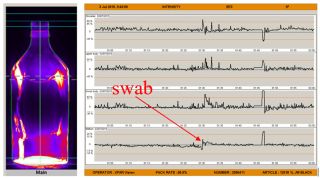
Controlling the glass distribution is the key to lighter and stronger bottles and jars, produced with (almost) zero defects at higher speed. Logically controlling the glass distribution does require continuous monitoring of bottles and jars produced, and evaluating every action on the IS machine against changes in glass distribution. In order to effectively manage the forming process glass distribution is THE reference.
Lowering disturbances: apply robot for swabbing
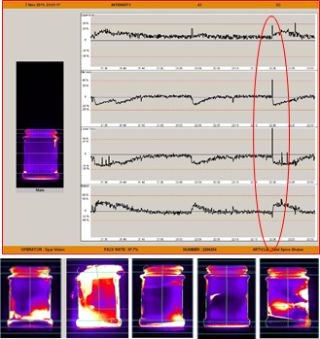
Disturbances as mentioned before are root causes for forming process variations (and this glass wall thickness variations and defects). It speaks for itself that lowering the level and frequency of disturbances will be of great help in realizing the ambition of lighter and stronger bottles produced with zero defects and higher speed.
For example, currently there is a lot of emphasis on swabbing. It is true that swabbing is one of the main disturbances in the glass making process. An example is given in figure 4. As such, swabbing is more a enemy than a remedy. Robot swabbing will for sure reduce forming process variations and is of great help to an operator. The BlankRobot of XPAR Vision swabs in a very consistent way the moulds and the neck rings. Therefor the variation in glass distribution (glass wall thickness) will be lower and critical defects due to swabbing will be zero. And due to automatic swabbing the operator has more time to concentrate on the quality of the bottle or jar.
Use of other sensors
Besides IR for bottle inspection and monitoring, nowadays also other sensors are available to be applied in the forming process. There are sensors which monitor the status of gob condition (weight, temperature, shape) at the area of gob cut, the status of gob loading (speed, length, time of arrival, position) just before the gob enters the mould and temperatures of parison, moulds, plunger and neck ring. All the data collected somehow relate to the quality of the bottle or jar produced. The more one knows about these relations, the higher the level of forming process control can be.
How to effectively lower glass wall thickness variations?
With the sensors mentioned so far the glass forming process is completely observed; one has enough information (data) of the forming process to be in control and to reduce the glass wall thickness variation. On most IS-machines the operator is responsible for the quality of the glass. All data given by all sensors must be processed by the operator and he must make the interpretation and conclusion: is the forming process still okay or is there any remedial action to be done? This is not an easy job, moreover because the operator is already fully occupied with swabbing the machine parts (50% of his time!), doing regular quality checks and changing wear out parts. Even for skilled people the interpretation of all the sensor data is difficult.
For example: the operator looks at the IR charts and see the IR-intensities for a certain cavity have been changed. In case he is well trained and experienced, he might conclude that the vertical glass distribution has been changed: the lower parts of the bottle are thicker and the neck/shoulder parts are thinner. This conclusion is right, but which remedial action should he take? Change the blank mould cooling? Change the contact time? Luckily, he has a sensor which measures parison temperature. From here he sees the parison temperature is increasing. But if he looks at the other cavities in the section, he sees normal parison temperatures. As a result he knows that mould cooling and contact time changes will not be an effective remedial action. So maybe gob loading? From the sensor measuring loading parameters he looks at the length of the gobs and sees a decreasing length of the gob in time. At the hit point of the deflector the coating is wear out and the friction is too high, which reduces the length of the gob. His conclusion now is to replace the deflector as the effective remedial action. And indeed, after the change of the deflector, the IR charts shows that the glass distribution is restored and the variation in the glass wall thickness reduced. But only for one cavity. Now the operator must look and deal with the other 35/47 cavities….due to the many other tasks he will not have enough time for this.
This example teaches us two important bottlenecks for reducing the glass variation:
- operator skills and experiences
- operator time spending limit
To give the operator more time to spend on the quality of the bottle and to reduce the variation a swabbing robot is a great help for the operator (besides his health and safety!).
The other bottleneck is the skills and experience of the operators. It takes a lot of training time and practice to utilize the potential benefit of the sensors. Also, nowadays experienced operators are leaving the companies for retirement and valuable know how is leaving the shop floor with them. In order to effectively reduce glass variation one should adapt to Process Artificial Intelligence.
Process Artificial Intelligence (AI)
The last decade the Artificial Intelligence has grown up to a mature technology. The breakthrough of AI is caused by new algorithms (methods) and increased computer power. The Process AI uses all the available sensor information and by means of the methods of AI the interpretation of all this sensor information is done automatically! The Process AI informs the operator that the glass forming process needs attention and provide the operator directly the right remedial action. If the operator performs this remedial action the glass variation will be quickly restored. As we look back to the example of the worn-out deflector with process AI: instead of doing the described interpretation steps, the operator directly gets the message: “please, change the deflector of cavity 11 M”.
In this way the glass forming will be stable (more output) and the glass distribution variations will be much lower (more quality). Because the Process AI continuously monitors all sensors information the detection of an anomaly in the glass forming process is much faster than with an operator. As such Process AI is a necessity for making a step wise change in the level of forming process control.
Automation
Another contribution is coming from automated control loops which compensate the drifting parameters of the glass forming process. A control loop uses the sensor data to see if the process variables are still at the set point values The sensor observes, analyzes and through feedback to the IS timing, the necessary adjustments are made. As the feedback is computer feedback, adjustments can be made within milliseconds. Even the very best operator/specialist will never be able to do this.
Within the past few years, (hot end) automated control loops have become available for controlling gob weight, ware spacing, mould temperature, plunger process and vertical glass distribution. It is to be expected that in the near future, more control loops will become available. Experience shows that all different control loops once applied basically have the same positive effect; the process variation is reduced and the bottles show less shift in glass distribution and have less defects. These control loops help the operator. But don’t forget that these automated control loops are not effective if the parts are wear out. In that case the operator must be noticed in time and replace the wear out parts.
Conclusion
In this article we have given a recipe for change in order to create a new world of container glass forming. In this new world with mainly machine interpretation and control by sensors, robots, data, artificial intelligence and automation, a step wise change in the level of forming process control will become feasible.
This step wise change in the level of forming process control pays off: with the right tools, focus and ambition, the container glass industry is able to do 25% better then today! Of course this step wise change will not happen overnight. Step by step one moves from more experienced base to more science based, and from more manual control to more automatic control.
And yes, this new environment for sure is more attractive for millenniums, and due to a higher level of automation health and safety is becoming less of a burden, and flexibility and complexity are better taken care of. But most importantly this “new” forming process creates bottles and jars with much less glass wall thickness variations and much higher efficiency levels. Lighter and stronger containers, produced with much less defects at higher speed and less human dependency are the result.